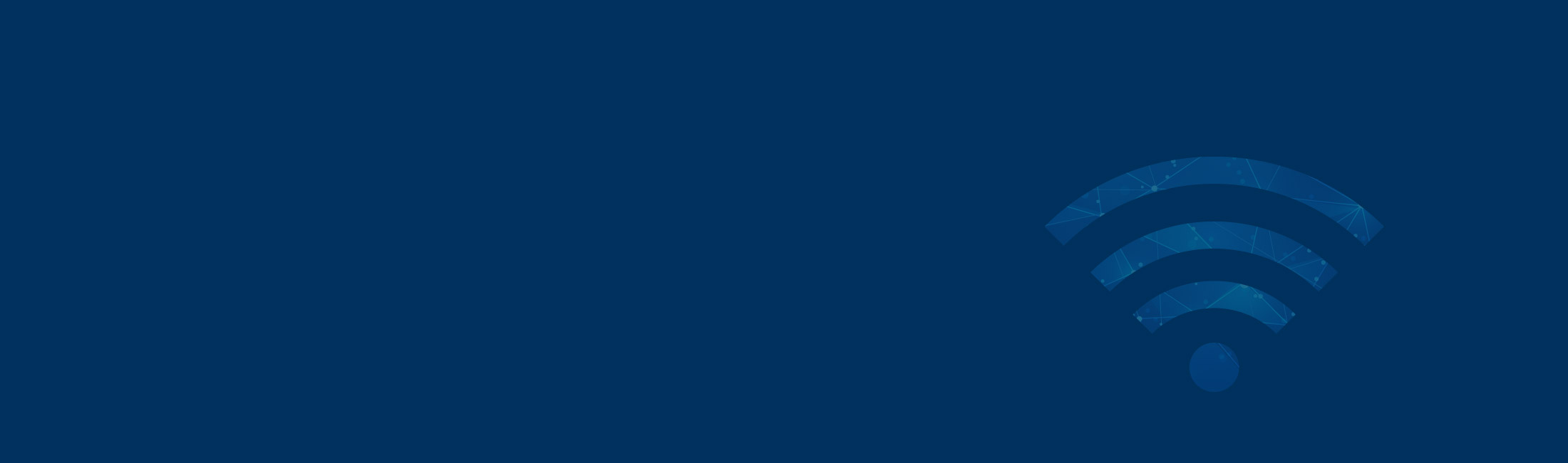
Newsroom
Company, Product, Event, and Industry News and Press
AGC Develops Process Digital Twin for Chemical Plants and Begins Operation at Vinyl Chloride Monomer Manufacturing Plant in Indonesia
AGC Inc. (AGC; Headquarters: Tokyo; President: Yoshinori Hirai), a world-leading manufacturer of glass, chemicals and high-tech materials, announced that the company had developed a Process Digital Twin for chemical plants. This technology will begin full-scale operation in April 2023 at the vinyl chloride monomer (VCM) manufacturing plant of P.T. Asahimas Chemical (Headquarters: Indonesia), its chemical manufacturing and sales subsidiary.
Process Digital Twin is a technology that reproduces the current state of a plant in a virtual space by importing operation data of an actual plant into a process simulator*2 in real time via a Plant Information Management System (PIMS)*1 and instantly performing high-speed calculations. By utilizing this system, data that could not be obtained or referred in real time can be estimated in the simulator to visualize operating conditions and asset performance. It is also expected to contribute significantly to stable plant operations by enabling instantaneous situational awareness and data-driven decision making.
The newly developed system covers a wide range of processes from reaction to distillation while incorporating the following innovations to realize high reproducibility of actual plants.
(1) A rigorous reaction model that takes into account even elementary reactions*3, which are the smallest reaction steps, and reproduces down to the behavior of by-products, a key to operational management.
(2) Dynamic simulation*4 reproduces not only the stable state of a plant but also the state in the process of change.
(3) Improved reproducibility of actual plant conditions by automatically correcting for changes in asset performance over time due to fouling and other effects based on actual data.
AGC is advancing DX at its chemical plants through the three steps of “Visualizing,” “Understanding,” and “Transforming.” As part of its efforts in “Visualizing,” AGC has introduced an integrated operation management system called “CHOPIN” and a private LTE network. As the next step after “Visualizing,” this initiative is to analyze the current status of plants using a Process Digital Twin (Understanding) and to achieve more advanced operations (Transforming).
In the future, AGC will roll out the technology to more plants, aiming to further stabilized operations by enhancing their sophistication.
AGC Group has formulated its medium-term management plan, AGC plus-2023 to achieve its long-term management strategy, “Vision 2030”, and one of the key directions in the plan is to boost competitiveness by accelerating DX. Until now, AGC Group has used digital technologies to transform business processes in areas such as manufacturing and development, sales and marketing, and logistics. AGC Group will continue to build its competitive advantage by transforming its business model by utilizing big data from every aspect of its operations and deliver new added value to its customers and to society.
*1 Plant Information Management System (PIMS): A database system that collects and stores plant operation data.
*2 Process simulator: A simulator that reproduce chemical plant state on a computer by calculations based on chemical engineering.
*3 Elementary reaction: The reaction of the smallest step that comprises a chemical reaction. The reaction that produces VCM is expressed by a combination of a large number of elementary reactions involving unstable chemical species called radicals.
*4 Dynamic simulation: Reproduction of dynamic changes in a plant through calculations.
Reference
Media inquiries
Chikako Ogawa, General Manager, Corporate Communications & Investor Relations Division
AGC Inc.
Contact: Fujiyama
TEL: +81-3-3218-5603